Safety and Health Management
NHK Spring Group's Basic Policy on Safety and Health
-
Safety takes precedence over everything else, and ensuring safety and health is a fundamental condition of a company.
-
Each and every employee will use creativity and ingenuity to effectively promote safety and health activities and create a safe, secure, and comfortable workplace with "zero accidents".
Promotion Structure
Organization Chart
Aiming for a comprehensive safety management system in the Company, the Central Safety and Health Council, chaired by the Vice President of NHK Spring, has been established at the top of the organization, under which a "Business Unit (BU)-based safety and health management system" has been set up for each production division, and a governance system has been established for all domestic and overseas companies, plants, and business sites.
General supervisor in each BU: Overseer of safety and health activities inside the BU (Corporate Officer and Division Vice President)
General safety officer in each BU: Implement actual activities under the BU general supervisor (Department Director/Deputy Director class)
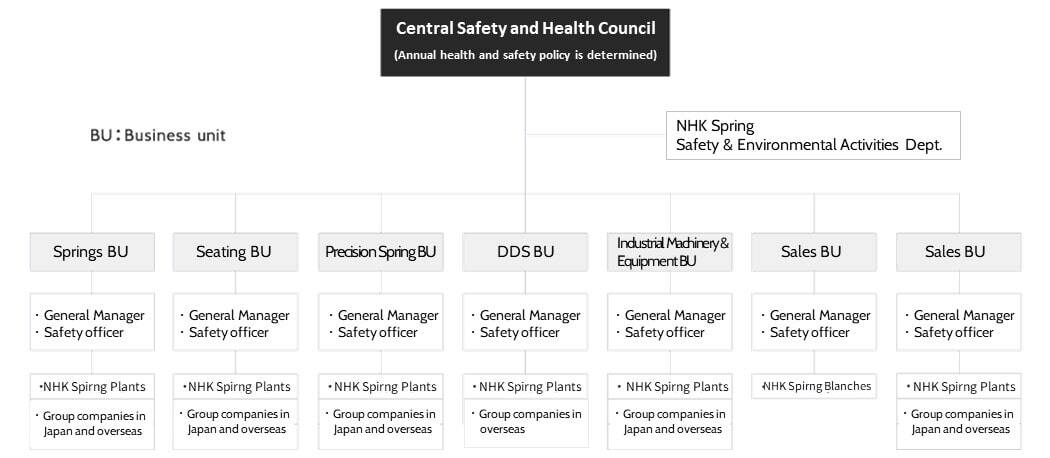
Management System
All manufacturing-related workplaces in Japan have introduced JISHA-style OSHMS and are implementing self-declarations.
Based on the annual safety and health activity policy, an annual activity plan is prepared for each business unit. Progress is managed at monthly meetings of the safety and health Committee.
Activities are checked, evaluated, and improved through internal safety and health audits (once a year).
Concrete Initiatives
Top management's own actions
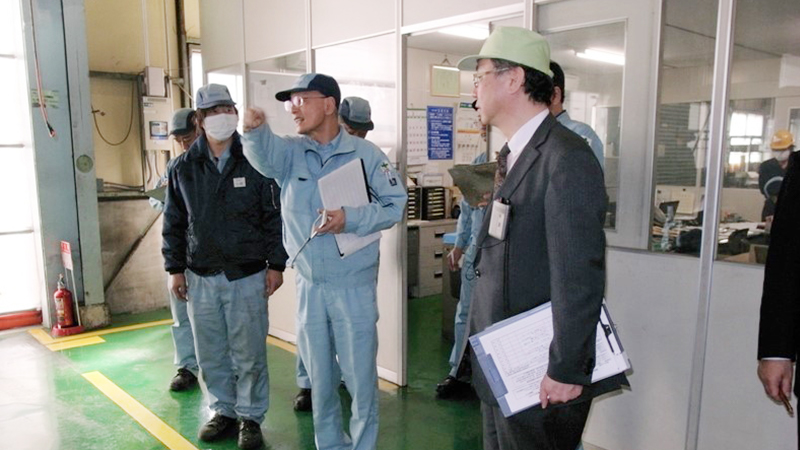
Top patrols
Once a year, by the end of June, all BUs systematically implement patrols.
Accident site inspections by top management
In the event of an industrial accident, the Central Safety and Health Council chairperson (Vice President) conducts an on-site inspection when deemed necessary.
Top management review
Conducted twice a year (first and second half).
-
Speeding-up of planning and decision-making for countermeasures and obtaining budgets.
-
Having top management personally visit a work site to confirm activities expedites safety measures at the work site, while at the same time greatly improving safety awareness among workers.
Realization of even more advanced equipment safety
We encourage employees to acquire Safety Assessor and Safety Sub-Assessor certificates in order to develop human resources who can promote the safety of machinery and equipment at production sites based on the latest safety knowledge and achieve high productivity.
In addition to introducing new equipment, they play a main role when revalidating existing equipment and conducting risk assessments. When occupational accidents occur, they provide countermeasures and advice from an expert's perspective.
Current qualifications: 2 Safety Assessors, 32 Safety Sub-Assessors (within NHK Spring)
Implementation of Safety and Health Training
-
Safety Dojo (each workplace)
-
Implementation of safety and health training in group/remote formats
-
Experiencing danger using VR
Implemented Activities
In-house commendation system
The award is given to workplaces in increments of 1,500 days.
(For a small plant, it takes a very long time to reach the record, which is calculated on a gross basis; 1,500 days without accident can be evaluated as about the same level of effort as a medium-sized plant receiving an award).
Frequency rate of absence (Graph)
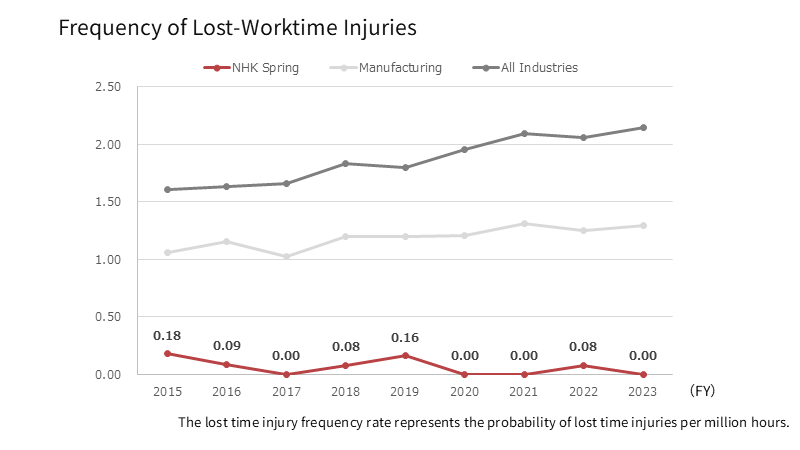